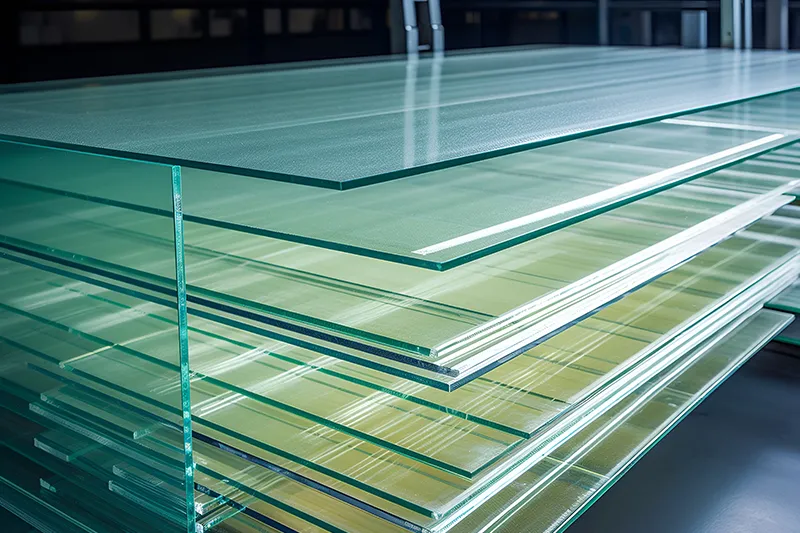
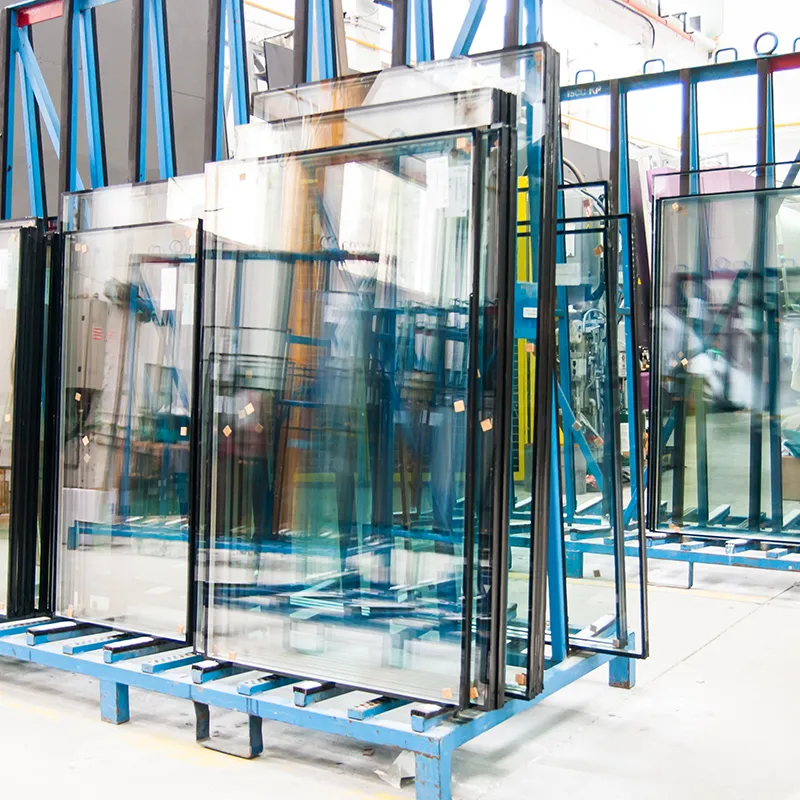
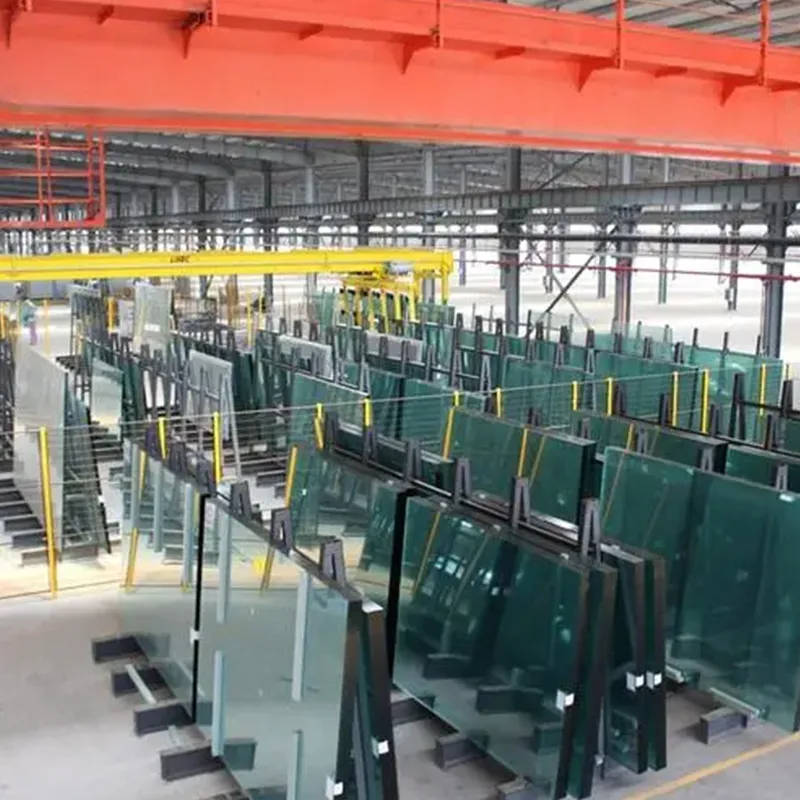
The traditional glass molding process can generally be divided into three steps: forming, annealing and cooling. During the glass forming process, the heating temperature and heating rate are closely related to the quality of the final glass product. Since most of the molding temperatures of glass are generally above 500°C, in order to avoid oxidation of the glass, the whole process needs to be carried out in an oxygen-free environment filled with nitrogen, so it is necessary to use nitrogen generator to produce nitrogen used in the forming process as protective gas, preventing the glass from being oxidized and contaminated. During the annealing and cooling stages, nitrogen has a significant effect on controlling the temperature distribution of the glass. The temperature inside the glass preform will be higher than the part exposed to nitrogen, which means that nitrogen can help control the temperature gradient, thus ensuring the quality and consistency of the glass. Especially during the cooling phase, this temperature gradient management is essential to avoid the build-up of stresses within the glass.
- During the glass forming process, nitrogen produced by nitrogen generator will flow through the glass forming chamber for gas purification in the manufacturing process, in order to create an ideal forming environment for molds and glass preforms.
- Our nitrogen generators can adjust the flow rate and purity of nitrogen according to the production demand, thus ensuring the flexibility and efficiency of the production process.
- Our nitrogen equipment can work continuously for a long time to support your glass processing and manufacturing, we can also utilize various methods to reduce the operating temperature to avoid the affect of high temperature to the equipment
-
- PSA Nitrogen Generators PSA nitrogen generation is a technology to separate nitrogen from air by the adsorption ability of carbon molecular sieve under pressure by air compressor. After the air is compressed and purified (removing the oil, water and dust, etc.) before transferring into the absorption tower filled with carbon molecular sieves (CMS), the oxygen molecule will be adsorbed by carbon molecular sieve, while nitrogen molecules are too large so that they will not be adsorbed. Read More
-
- Modular Nitrogen Generator Our modular nitrogen generator has a compact structure, adopting non-pressure container molded in aluminum alloy die-casting and pipeline made of high strength alloy steel with quick-connect fittings. The installation process is convenient with no need for extra painting. Read More
-
- PSA Oxygen Generator Two adsorption tower will be installed in parallel in PSA oxygen generator, one tower begins the adsorption phase while other tower regenerates by de-pressurizing. The PLC controller manages process valves with built-in logic for an automatic stop/start for continuous oxygen production. Read More
-
- VPSA Oxygen Generator Our VPSA oxygen generator is able to generate oxygen with purity between 90% and 95%. It is mainly composed of air blower, vacuum bump, switching valve and oxygen buffer tank. The production cost of using this VPSA oxygen generator will decrease as the production volume increases, which makes it suitable for applications like medium and large industrial systems where continuous supply of high purity oxygen is required. Read More